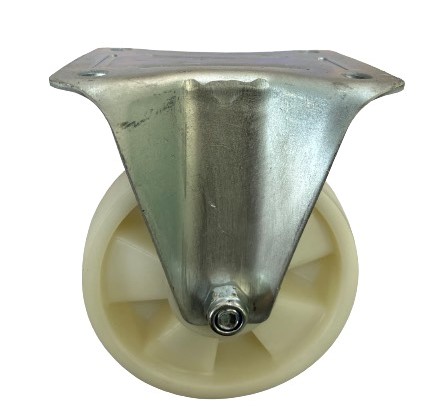
Castor wheel manufacturers play a vital role in ensuring the quality and reliability of industrial caster wheels, which are essential components in various industries. While these wheels may seem simple, their design, materials, and manufacturing processes undergo rigorous scrutiny to meet high standards of performance and durability. In this blog, we’ll delve into the behind-the-scenes processes of castor wheel manufacturers, exploring how they ensure quality and reliability in their products.
Understanding Industrial Caster Wheels
Before delving into the manufacturing process, it’s essential to understand the significance of industrial caster wheels. These wheels are designed to provide mobility and support for heavy loads in industrial environments such as warehouses, factories, hospitals, and airports. They come in various sizes, load capacities, and configurations to suit different applications, from light-duty carts to heavy-duty machinery.
Material Selection
One of the key factors in ensuring the quality and reliability of industrial caster wheels is material selection. Castor wheel manufacturers carefully choose materials that offer the necessary strength, durability, and resistance to wear and tear. Common materials used in caster wheel manufacturing include:
– Polyurethane: Known for its abrasion resistance, polyurethane is often used in caster wheels for smooth and quiet operation, making it ideal for indoor applications.
– Rubber: Rubber caster wheels provide shock absorption and traction, making them suitable for outdoor and rough terrain applications.
– Nylon: Nylon caster wheels are lightweight and resistant to chemicals, making them ideal for corrosive environments such as laboratories and food processing facilities.
– Steel: Steel caster wheels offer exceptional strength and durability, making them suitable for heavy-duty industrial applications where load capacity is critical.
Design and Engineering
Once the materials are selected, castor wheel manufacturers focus on design and engineering to optimize performance and reliability. This includes:
– Load Capacity: Designing caster wheels with the appropriate load capacity to support the intended application without compromising safety or performance.
– Wheel Diameter: Determining the optimal wheel diameter based on load requirements, surface conditions, and maneuverability needs.
– Bearing Type: Selecting the appropriate bearing type (such as ball bearings or roller bearings) to ensure smooth and efficient rolling motion.
– Mounting Configuration: Designing caster wheels with the appropriate mounting configuration (such as plate, stem, or threaded stem) to facilitate easy installation and compatibility with existing equipment.
Manufacturing Process
The manufacturing process of industrial caster wheels involves several steps to ensure quality and reliability:
1. Molding: For materials like polyurethane and rubber, the manufacturing process begins with molding the raw material into the desired wheel shape using molds and presses.
2. Injection Molding: Some caster wheel components, such as bearing housings and mounting plates, may be produced using injection molding techniques for precise and consistent results.
3. Machining: After molding, caster wheel components undergo machining processes such as turning, milling, and drilling to achieve the final dimensions and specifications.
4. Assembly: Once all components are manufactured, they are assembled together to create the final caster wheel assembly. This may include pressing bearings into housings, attaching mounting plates, and securing wheels to axles.
5. Quality Control: Throughout the manufacturing process, castor wheel manufacturers implement rigorous quality control measures to ensure that each wheel meets the specified standards for performance, durability, and safety. This may involve testing for load capacity, rolling resistance, and durability under various conditions.
Testing and Certification
Before industrial caster wheels are released to the market, they undergo extensive testing and certification to ensure compliance with industry standards and regulations. This may include:
– Load Testing: Subjecting caster wheels to load testing to verify their load capacity and durability under specified conditions.
– Rolling Resistance Testing: Evaluating the rolling resistance of caster wheels to ensure smooth and efficient operation.
– Environmental Testing: Testing caster wheels for resistance to temperature extremes, moisture, chemicals, and other environmental factors.
– Certification: Obtaining certifications such as ISO 9001 and ANSI/BIFMA to demonstrate compliance with quality management and performance standards.
Castor wheel exporters in India
Castor wheel exporters in India supply high-quality wheels for diverse industries globally. With a wide range of options, including heavy-duty and specialty wheels, these exporters offer reliable solutions for material handling needs. They ensure timely delivery and excellent customer service to meet international demands effectively.
Conclusion
In conclusion, castor wheel manufacturers play a crucial role in ensuring the quality and reliability of industrial caster wheels. Through careful material selection, design and engineering, and rigorous manufacturing processes, they produce wheels that meet high standards of performance, durability, and safety. By understanding the behind-the-scenes processes involved in caster wheel manufacturing, businesses can make informed decisions when selecting wheels for their applications, ensuring optimal mobility, support, and reliability in industrial environments.