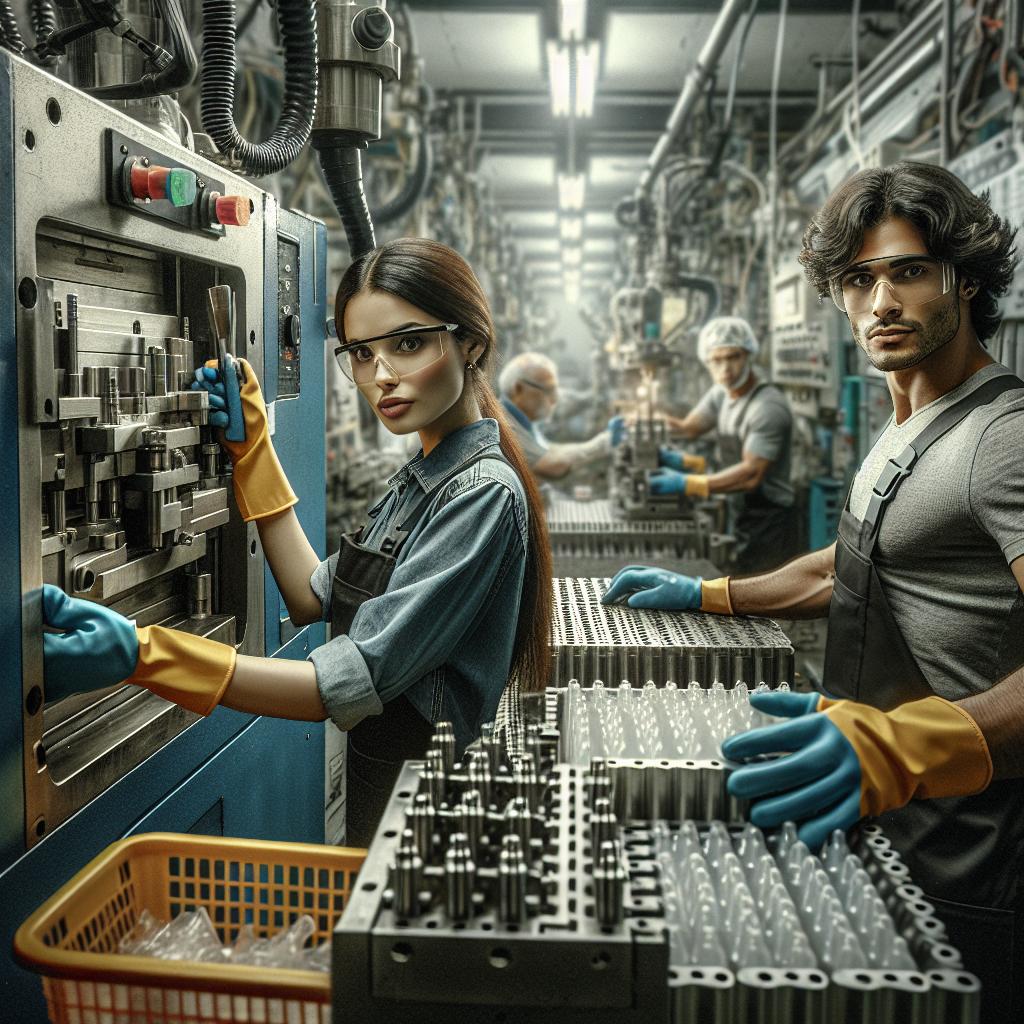
Injection molding remains a highly efficient manufacturing process, renowned for its ability to produce large quantities of parts with consistent quality. This method involves the high-pressure injection of molten material into a mold, which is then cooled to form the desired part. As companies seek ways to economize production without compromising on quality, China injection molding emerges as a compelling solution. The country’s manufacturing landscape offers a unique blend of cost-efficiency and scalability, attributes that are critical for businesses looking to maintain a competitive edge in the market.
The allure of injection molding in China lies not just in its affordability but also in the comprehensive services that accompany the manufacturing process. Companies can expect integrated solutions that cover design, prototyping, and mass production, all tailored to reduce costs and streamline operations. Furthermore, advancements in technology have bolstered the efficiency and precision of Chinese injection molding, enhancing its appeal to businesses worldwide. Assessing the balance between cost and quality becomes crucial for any enterprise considering injection molding services in China.
Advantages of Injection Molding in China
The strategic implementation of injection molding in China holds numerous advantages for businesses looking to maximize their production efficacy. The region’s candidacy as a manufacturing hub is fortified by its competitive pricing, which significantly undercuts costs on a global scale. This cost advantage is particularly pronounced in the realm of injection molding, where Chinese manufacturers have mastered the art of delivering high-volume orders at reduced rates. Companies tapping into this cost-saving potential can reallocate funds towards innovation, marketing, or other core business areas, thereby achieving a more robust financial standing.
Moreover, the scalable nature of China’s injection molding services permits businesses to adjust their production based on market demands, ensuring they are never burdened with excess inventory. The presence of a well-developed industrial infrastructure, coupled with a dense network of suppliers, streamlines the production lifecycle from raw material procurement to final output. This efficient supply chain is pivotal in reducing lead times, enabling faster turnaround for products and enhancing market responsiveness. With such streamlined processes, injection molding in China not only augments cost savings but also significantly improves a company’s ability to respond to consumer needs with agility.
Factors Affecting Cost-Effectiveness
The attractive pricing model of injection molding in China is a composite of various economic factors, all contributing to a more cost-effective process. A primary component is the economies of scale achieved by Chinese manufacturers. With large-scale production facilities, the cost per unit diminishes as volume increases. This scalability allows businesses to drive down expenses substantially when ordering in bulk, optimizing their overall investment in production. Additionally, the competitive nature of the Chinese market encourages manufacturers to constantly innovate, further cutting costs and enhancing efficiency.
Labor costs also play a crucial role in the cost-effectiveness equation. Chinese manufacturers can offer more competitive labor rates compared to many other countries, translating into lower overall manufacturing costs. This does not inherently mean a compromise in quality; skilled labor is abundant in China due to its focused industrial training programs.
However, global companies must consider their entire operational footprint, taking into account export fees, tariffs, and freight costs, to fully understand the financial benefits. Balancing these aspects with the advantages that local production might offer leads to a comprehensive analysis of cost-effectiveness. Therefore, while China’s injection molding sector presents clear merits in terms of production costs, companies must weigh all variables to arrive at an informed decision
Quality Considerations
Engaging in injection molding in China comes with quality considerations that businesses must navigate. A lingering stereotype paints Chinese manufacturing as inferior. However, this perception doesn’t hold true across the board. Many Chinese injection molding plants hold international quality certifications, showcasing their commitment to excellence. These manufacturers adhere to stringent quality control protocols, ensuring that every batch of products meets both international standards and customer expectations.
It’s essential for businesses to conduct due diligence when selecting a Chinese manufacturing partner. This involves vetting their quality assurance processes, from raw material inspection to final product testing. Effective communication and clear specification of standards can mitigate the risk of subpar production outcomes. Establishing a solid quality agreement with the manufacturer can provide additional security, outlining the protocols to be followed and the remediation steps in the event of quality issues. Guaranteeing quality in the output from injection molding operations in China is a manageable challenge, provided that companies are thorough in their vetting processes and communicate their quality needs explicitly.
Logistics and Efficiency
When dissecting the logistical aspect of China’s injection molding industry, efficiency stands out as a key benefit. China’s logistical network is robust and mature, built upon decades of manufacturing and exporting on a grand scale. This network streamlines the movement of goods, significantly reducing the time from factory floor to global markets. The presence of major shipping ports and an extensive freight system enables manufacturers to export products with remarkable speed and reliability, which is crucial for maintaining supply chain momentum.
Moreover, the procedural efficiency of China’s injection molding operations presents further advantages. Chinese manufacturers have embraced automation and state-of-the-art technologies to minimize human error and speed up production cycles. These smart-manufacturing tactics are not only time savers but also allow for a heightened level of precision in the manufacturing process. The integration of modern technology in logistics and production underscores China’s commitment to efficient manufacturing practices. For businesses, this translates into faster product launches and the agility to respond to consumer demand, providing a competitive advantage in fast-paced markets. To fully capitalize on these logistical strengths, companies must navigate and comply with export regulations, ensuring smooth and efficient transit of goods.
Key Takeaway
China injection molding presents a viable, cost-effective manufacturing solution for businesses looking to optimize their production costs. The combination of competitive pricing, economies of scale, and efficient logistical networks positions China as a compelling choice for companies globally. While there are quality and operational factors to consider, the advances in technology and stringent quality control standards within China’s manufacturing landscape mitigate these concerns considerably.
Businesses exploring China injection molding should expect not just financial benefits but also a partnership that affords scalability and market responsiveness. Conducting thorough research and maintaining clear communication with Chinese manufacturers are essential to harnessing the full potential of this manufacturing approach. Ultimately, with an informed approach and strategic planning, companies can look forward to a fruitful collaboration that bolsters their market position with effective, high-quality production outcomes.