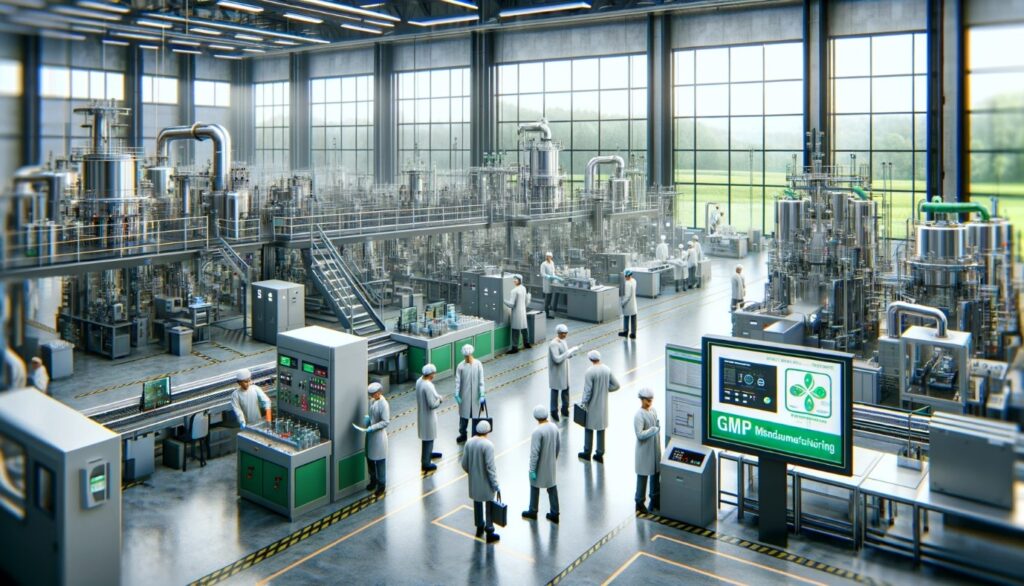
I. Introduction
A. Importance of Quality Assurance in Manufacturing:
Quality assurance is paramount in manufacturing to ensure products meet specifications and customer expectations. It involves systematic processes to prevent defects and maintain consistency in production. Effective quality assurance enhances product reliability, customer satisfaction, and brand reputation while reducing costs associated with defects and recalls.
B. Overview of GMP Certification and its Significance:
Good Manufacturing Practice (GMP) Certification is a quality assurance standard that ensures products are consistently produced and controlled according to quality standards. GMP Certification is crucial in industries such as pharmaceuticals, food, and cosmetics to guarantee product safety, efficacy, and compliance with regulatory requirements. It signifies a commitment to quality and enhances consumer trust and confidence in products.
II. Understanding GMP Certification
A. What is GMP Certification?
GMP Certification is a quality assurance designation that ensures products are manufactured, stored, and distributed consistently and in accordance with quality standards. It verifies that manufacturing processes meet specific requirements to produce safe and effective products, particularly in industries such as pharmaceuticals, food, and cosmetics.
B. Key Principles and Requirements of GMP:
GMP encompasses principles and requirements that govern manufacturing practices to ensure product quality and safety. These include adherence to hygiene, cleanliness, documentation, validation of processes, equipment maintenance, and personnel training. Compliance with these principles is essential to mitigate risks and maintain product integrity throughout the manufacturing process.
C. Benefits of GMP Certification for Businesses:
GMP Certification offers numerous benefits for businesses, including enhanced product quality, compliance with regulatory requirements, improved consumer confidence, reduced risk of product recalls, and increased market access. It demonstrates a commitment to quality and safety, fostering trust with customers and stakeholders and providing a competitive advantage in the marketplace.
III. Getting Started with GMP Certification
A. Steps to Attain GMP Certification:
The journey to GMP Certification involves several key steps. Firstly, thoroughly familiarize yourself with GMP requirements and standards applicable to your industry. Next, identify and assess your organization’s current practices against GMP criteria to determine areas for improvement. Develop a comprehensive plan outlining the steps needed to achieve compliance and allocate necessary resources.
B. Planning and Preparation for GMP Implementation:
Effective planning is essential for successful GMP implementation. Establish clear objectives, define roles and responsibilities, and allocate resources accordingly. Develop a detailed implementation plan with timelines, milestones, and deliverables. Consider factors such as personnel training, equipment upgrades, and documentation requirements. Effective planning ensures smooth implementation and streamlines the path towards GMP Certification.
C. Conducting a Gap Analysis and Assessing Compliance:
Conduct a thorough gap analysis to identify disparities between current practices and GMP requirements. Assess existing processes, procedures, and documentation against GMP standards to pinpoint areas needing improvement. Determine the level of compliance with GMP criteria and prioritize corrective actions accordingly. Regularly review and update the gap analysis to track progress and ensure ongoing alignment with GMP principles.
IV. Implementing GMP Standards
A. Establishing GMP-compliant Processes and Procedures:
Implementing GMP-compliant processes and procedures involves defining and documenting protocols for all stages of manufacturing, storage, and distribution. This includes ensuring adherence to hygiene, sanitation, and quality control measures, as well as implementing protocols for handling deviations and ensuring product integrity throughout the production process.
B. Documentation and Record-Keeping Requirements:
GMP standards require comprehensive documentation and record-keeping to track and trace all aspects of the manufacturing process. This includes maintaining detailed records of production activities, equipment maintenance, quality control tests, and personnel training. Documentation ensures transparency, accountability, and compliance with regulatory requirements, facilitating audits and inspections to demonstrate GMP compliance.
C. Training and Education for GMP Compliance:
They are vital components of GMP compliance, ensuring that personnel understand their roles and responsibilities in maintaining product quality and safety. Training programs should cover GMP principles, procedures, and best practices, as well as specific job-related tasks and responsibilities. Ongoing education and training are essential to keep personnel informed about updates to GMP standards and reinforce compliance efforts throughout the organization.
V. Auditing and Certification Process
The auditing and certification process is a critical aspect of ensuring compliance with Good Manufacturing Practice (GMP) standards, which are essential for maintaining product quality and safety in industries such as pharmaceuticals, food, and cosmetics.
Internal Audits:
Internal audits are conducted by organizations to assess their compliance with GMP standards and identify areas for improvement. Trained auditors review processes, procedures, and documentation to ensure adherence to GMP principles. Internal audits help organizations proactively address issues and maintain continuous improvement in their quality management systems.
External Audits:
External audits are conducted by independent certification bodies to evaluate an organization’s compliance with GMP standards. Accredited auditors assess the organization’s processes, procedures, and facilities to determine if they meet the requirements for GMP certification. External audits provide unbiased verification of GMP compliance and are necessary for obtaining GMP certification.
Preparing for Audits:
Prior to audits, organizations must prepare thoroughly by ensuring all documentation and records are up-to-date and readily accessible. They should conduct internal audits to identify and address any non-conformities and implement corrective actions as needed. Training employees on audit procedures and expectations helps ensure a smooth audit process.
Audit Findings and Corrective Actions:
During audits, findings may be identified that require corrective action to address non-conformities or areas for improvement. Organizations must promptly investigate audit findings, determine root causes, and implement corrective actions to prevent recurrence. Documenting and tracking corrective actions is essential to demonstrate continuous improvement and compliance with GMP standards.
Obtaining GMP Certification:
After successful completion of external audits and corrective actions, organizations can apply for GMP certification from accredited certification bodies. Certification demonstrates the organization’s commitment to quality and compliance with GMP standards, enhancing credibility and trust with customers, regulators, and stakeholders.
VI. Maintaining GMP Certification
A. Continuous Improvement Strategies for GMP Compliance:
Continuous improvement is essential for maintaining GMP certification. Organizations should regularly review and update their processes, procedures, and systems to address emerging risks and improve efficiency. Implementing feedback mechanisms, conducting periodic audits, and fostering a culture of innovation and learning are key strategies for achieving continuous improvement in GMP compliance.
B. Monitoring and Evaluation of GMP Systems:
Effective monitoring and evaluation mechanisms are crucial for ensuring the ongoing effectiveness of GMP systems. Organizations should establish procedures for monitoring key performance indicators, conducting regular inspections, and assessing the performance of GMP controls. This enables timely identification of issues and opportunities for improvement, facilitating proactive measures to maintain GMP certification.
C. Addressing Non-Conformities and Taking Corrective Actions:
Promptly addressing non-conformities and implementing corrective actions is vital for maintaining GMP certification. Organizations should establish procedures for reporting, investigating, and resolving non-conformities identified during audits, inspections, or quality control processes. By taking swift and effective corrective actions, organizations demonstrate their commitment to maintaining GMP compliance and ensuring product quality and safety.
VII. Industry-Specific Considerations for GMP Certification
A. GMP Certification in Pharmaceutical Manufacturing:
GMP certification is critical in pharmaceutical manufacturing to ensure the safety, efficacy, and quality of medicinal products. Specific considerations include stringent control over raw materials, manufacturing processes, and packaging, as well as compliance with regulations such as Good Laboratory Practice (GLP) and Good Distribution Practice (GDP) to safeguard product integrity throughout the supply chain.
B. GMP Certification in Food and Beverage Industry:
In the food and beverage industry, GMP certification is essential for ensuring the safety and quality of consumable products. Key considerations include hygiene practices, sanitation procedures, and traceability measures to prevent contamination and ensure compliance with food safety regulations such as Hazard Analysis and Critical Control Points (HACCP) and Food Safety Modernization Act (FSMA).
C. GMP Certification in Cosmetics and Personal Care Products:
GMP certification is vital in the cosmetics and personal care products industry to guarantee the safety and integrity of skincare, haircare, and beauty products. Industry-specific considerations encompass formulation control, ingredient sourcing, packaging hygiene, and product labeling compliance with regulations such as Cosmetic Product Safety Reports (CPSR) and European Union Cosmetics Regulation (EC) No. 1223/2009.
VIII. Conclusion
A. Recap of GMP Certification Importance and Benefits:
GMP certification plays a vital role in ensuring product quality, safety, and compliance with regulatory standards. It offers numerous benefits, including enhanced credibility, consumer trust, and market access. By achieving GMP certification, organizations demonstrate their commitment to quality assurance and meet the expectations of customers and stakeholders.
B. Encouragement for Pursuing GMP Certification:
For organizations seeking to excel in their respective industries, pursuing GMP certification is a strategic decision that can lead to improved product quality, regulatory compliance, and competitive advantage. Embracing GMP principles fosters a culture of quality and continuous improvement, driving organizational success and customer satisfaction.
C. Final Thoughts on Quality Assurance and Continuous Improvement:
Quality assurance and continuous improvement are integral to the success of any organization. GMP certification serves as a framework for achieving excellence in product quality, safety, and compliance. By prioritizing quality assurance practices and embracing a mindset of continuous improvement, organizations can enhance their reputation, mitigate risks, and sustain long-term success in today’s dynamic business environment.