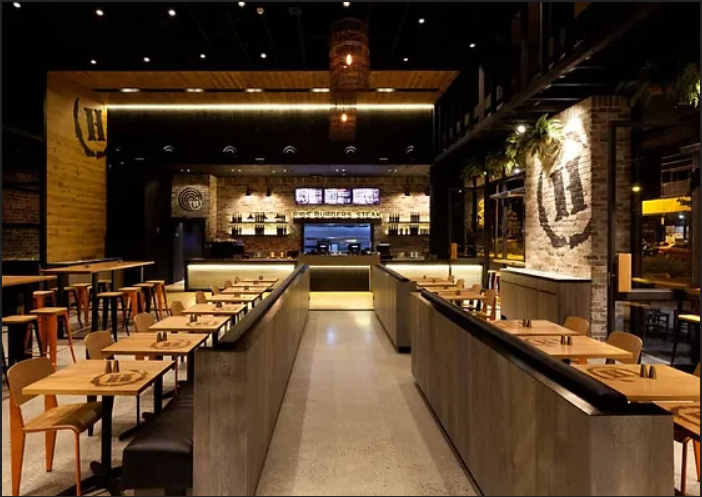
Formwork is a critical aspect of construction that provides temporary support to structures during the concreting process, ensuring they take the correct shape until the concrete gains sufficient strength. While the installation of formwork is an essential stage of construction, its dismantling—or striking—is equally significant and often carries a range of risks. Unsafe formwork dismantling can lead to accidents, project delays, and even structural failure. For construction sites across Australia, particularly in rapidly growing cities like Sydney, adhering to best practices during formwork removal is essential for both safety and project efficiency.
Let us take a closer look into the best practices for safe formwork dismantling, with a focus on Australian sites. We will also explore a case study where safe formwork practices resolved a potentially hazardous situation, as well as cover the role of experienced formwork contractors near Sydney in ensuring these safety standards are met.
The Importance of Safe Formwork Dismantling
Concreting formwork plays an essential role in maintaining structural integrity while concrete sets. However, the process of striking the formwork poses significant risks, particularly in terms of worker safety. Falling formwork panels, unbalanced structures, and unstable loads can lead to injuries or fatalities if proper precautions aren’t in place.
Australian Work Health and Safety (WHS) regulations require that construction companies mitigate risks through detailed planning, communication, and the use of proper techniques when dismantling formwork. Key hazards during this stage include:
- Collapse of partially dismantled formwork
- Falling materials or tools
- Instability of the structure once formwork is removed
- Human error or lack of training among workers
These risks underscore the importance of following best practices, as any failure to do so can have catastrophic consequences.
Best Practices for Safe Formwork Dismantling
1. Comprehensive Planning and Preparation
Proper planning is the foundation of safe formwork dismantling. Before work begins, contractors must develop a formwork striking plan that aligns with WHS regulations and considers the specifics of the site, structure, and type of formwork used. This plan should include:
- Detailed steps outlining the dismantling process
- Timeline considerations to ensure that concrete has reached the required strength before striking
- Identification of potential hazards and mitigation strategies
- Clear roles and responsibilities for each worker involved in the dismantling process
2. Adequate Curing Time
One of the most critical factors in determining when to dismantle formwork is the curing time of the concrete. Australian standards typically require concrete to achieve at least 70% of its compressive strength before formwork is removed. The time it takes for concrete to cure depends on factors such as:
- Concrete mix. Different mixes may require varying curing times.
- Weather conditions. Higher humidity and cooler temperatures can slow the curing process.
- Load-bearing requirements. Structural components that will bear significant loads may require a longer curing period to reach their full strength.
Formwork contractors near Sydney must carefully monitor these factors and confirm the concrete’s strength before proceeding with any dismantling.
3. Proper Sequence of Dismantling
The sequence in which formwork is struck plays a crucial role in maintaining stability during the process. Removal should always be carried out from the top down, following the reverse order of installation. Key considerations include:
– Striking should start with non-load-bearing formwork.
– Horizontal supports should be removed before vertical supports.
– Careful attention should be paid to load redistribution as formwork is removed.
Following these principles reduces the risk of sudden collapse or structural instability.
4. Use of Appropriate Equipment
The use of proper tools and equipment for dismantling formwork is essential for safety. This includes scaffolding, ladders, and mechanical lifting equipment, such as cranes, for large or heavy formwork sections. Equipment should be inspected regularly for wear and tear to prevent failures during use.
Workers must be trained in the proper use of this equipment to avoid mishaps. All lifting devices must be capable of supporting the loads associated with dismantling activities, and any damaged or defective equipment should be removed from service immediately.
5. Skilled Workforce and Continuous Training
Even the best-laid plans will fail if the workforce is not adequately trained in formwork dismantling techniques. Formwork contractors should ensure that all workers are familiar with the specific formwork system in use, including its design, assembly, and disassembly process. Training should include:
- Safe work procedures for formwork dismantling
- Hazard identification and risk management strategies
- Proper use of personal protective equipment (PPE)
- Emergency response protocols in the event of an accident
Continuous training is essential to keeping up with evolving safety standards and the introduction of new formwork systems. For instance, formwork contractors near Sydney often participate in industry workshops and safety training courses to stay updated on best practices.
6. Monitoring and Communication During the Process
During the dismantling process, clear communication between all team members is vital. Supervisors should monitor the work to ensure that each step of the plan is followed and that any unexpected issues are addressed promptly. Workers should use signalling or two-way communication devices to report any concerns or hazards in real-time.
Additionally, safety officers should inspect the work area periodically to confirm that all dismantling activities adhere to safety standards and that no unauthorised personnel are in the vicinity.
Case Study: Avoiding Disaster through Safe Formwork Practices
In 2018, a construction project in Western Sydney involving a multi-story commercial building encountered a significant challenge during the dismantling of its formwork system. The project used large-scale modular formwork for the concrete floors, and the team was eager to speed up the process to meet deadlines. However, as they prepared to strike the formwork for the upper floors, engineers detected that the concrete had not fully cured due to the unusually humid weather conditions that had delayed the drying process.
Recognising the potential for collapse if the formwork was removed prematurely, the site manager halted the dismantling and called in a team of expert formwork contractors near Sydney to reassess the situation. The contractors conducted a series of tests on the concrete to measure its compressive strength and found it to be well below the required levels for safe removal.
Working with the site’s structural engineers, the formwork contractors developed a revised plan that delayed the striking process by an additional week, allowing the concrete to cure fully. They also reinforced critical load-bearing sections with temporary supports to prevent any chance of collapse. Furthermore, they introduced continuous monitoring of the weather and concrete curing process to ensure no similar delays would be overlooked in the future.
Through these cautious and informed practices, the team avoided what could have been a catastrophic structural failure. Instead, the project was completed without incident, with the formwork contractors’ expertise ensuring that all safety regulations were adhered to.
Role of Formwork Contractors Near Sydney
Sydney’s booming construction sector relies on experienced formwork contractors who understand the complexities of both formwork installation and dismantling. These contractors play a crucial role in minimising risk by:
- Conducting detailed site assessments. Before dismantling, contractors assess the site to identify potential hazards, such as uneven ground or nearby structures that could be affected.
- Providing skilled labour. Experienced teams know how to handle complex formwork systems, ensuring that dismantling is carried out safely and efficiently.
- Offering specialised equipment. Contractors bring in the right tools and machinery to facilitate safe removal, reducing the risk of accidents caused by manual handling.
By working with qualified formwork contractors, construction companies can ensure that their formwork dismantling processes meet the highest safety standards and comply with WHS regulations.
Conclusion
Dismantling concreting formwork is a high-risk activity that requires careful planning, skilled labour, and strict adherence to safety standards. Australian construction sites, particularly in fast-growing areas like Sydney, face the challenge of maintaining worker safety while balancing project deadlines. By following best practices such as comprehensive planning, proper curing times, and the use of skilled formwork contractors, companies can mitigate the risks associated with formwork dismantling.
Ultimately, investing in safety protocols not only protects workers but also ensures the long-term success and structural integrity of construction projects. With the right approach, the hazards of formwork dismantling can be effectively managed, as demonstrated in the case study where safe practices averted a potential disaster. For construction firms operating in Sydney, partnering with knowledgeable formwork contractors can make all the difference in maintaining a safe and successful project.