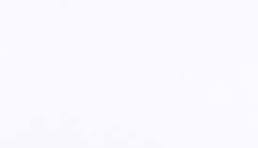
Aluminium sulfate, a vital chemical compound, finds extensive application in various industries, including water treatment, paper manufacturing, and the production of fire extinguishers. Understanding the production costs associated with aluminium sulfate is pivotal for manufacturers and stakeholders across these sectors. This article aims to delve into the factors influencing the aluminium sulfate production cost and its implications.
Raw Materials:
The production cost of aluminium sulfate is significantly influenced by the cost of raw materials utilized in its synthesis. The primary raw materials required for aluminium sulfate production include:
-
Aluminium Source: The primary source of aluminium for aluminium sulfate production is typically bauxite ore or aluminium hydroxide. The cost of the aluminium source fluctuates based on factors such as purity, availability, and transportation logistics.
-
Sulfuric Acid: Sulfuric acid serves as a key reagent in the production of aluminium sulfate. The cost of sulfuric acid is influenced by factors such as concentration, purity, production method, and market demand.
Request For Free Sample: https://www.procurementresource.com/production-cost-report-store/aluminium-sulfate
Manufacturing Process:
The production cost of aluminium sulfate is also influenced by the complexity of the manufacturing process. The synthesis of aluminium sulfate typically involves the following steps:
-
Reaction: The aluminium source, such as bauxite ore or aluminium hydroxide, is reacted with sulfuric acid to produce aluminium sulfate. This reaction may occur in batch reactors or continuous flow systems, each with its associated equipment and operational costs.
-
Filtration and Separation: After the reaction, the resulting mixture is typically filtered to separate the solid aluminium sulfate product from the reaction by-products and unreacted materials. Filtration processes require filtration equipment, filter media, and energy for operation.
-
Drying and Packaging: The filtered aluminium sulfate product is dried to remove excess moisture and packaged for distribution. Drying processes involve energy consumption for heating and drying equipment.
Energy Costs:
Energy costs, including electricity and heat, constitute a significant portion of the production cost of aluminium sulfate. The manufacturing process involves energy-intensive operations such as heating, mixing, filtration, and drying. Energy-efficient technologies and optimization of process parameters can help reduce energy consumption and lower production costs.
Environmental Considerations:
Compliance with environmental regulations and sustainability initiatives also impacts the production cost of aluminium sulfate. Manufacturers must adhere to environmental standards governing emissions, waste management, and resource utilization. Investments in pollution control measures, waste treatment technologies, and sustainability initiatives add to the overall production costs.
Economies of Scale:
Economies of scale play a significant role in determining production costs. Larger-scale production facilities benefit from lower unit costs due to spreading fixed costs over a higher volume of production. Manufacturers may consider scaling up production capacity to achieve cost efficiencies and reduce production costs per unit of aluminium sulfate.
Conclusion:
In conclusion, the production cost of aluminium sulfate is influenced by various factors, including raw material costs, manufacturing process complexity, energy costs, environmental considerations, and economies of scale. Manufacturers and stakeholders in industries reliant on aluminium sulfate must carefully evaluate these factors and implement strategies to optimize production costs while maintaining product quality, compliance with regulations, and sustainability goals. By understanding the factors affecting production costs, manufacturers can make informed decisions to enhance competitiveness and ensure affordability and accessibility of aluminium sulfate in the market.